In recent years, 3D printing has emerged as a transformative technology across multiple industries, from aerospace to healthcare. It has been hailed as a potential game-changer in fields that rely on precision, customization, and rapid prototyping. The watchmaking industry, known for its long-standing tradition of meticulous craftsmanship, is no exception to this trend. The question that arises, however, is whether 3D printing technology can truly revolutionize the watchmaking process, a process that has been honed over centuries to perfection.
In this article, we will explore the potential of 3D printing in watchmaking, examining its impact on design, production, materials, and overall watchmaking philosophy. Can it replace traditional methods? Or will it merely serve as a complementary tool in the hands of expert watchmakers? We will consider both the opportunities and challenges presented by 3D printing, evaluating whether it can truly live up to the promise of revolutionizing the craft of horology.
1. The Traditional Watchmaking Process: A Brief Overview
To understand the potential impact of 3D printing on the watchmaking industry, it’s essential first to appreciate the complexity of traditional watchmaking. Creating a luxury mechanical watch involves an intricate series of steps, each requiring precise craftsmanship and attention to detail.
a. Design and Engineering
The design process is where the watchmaking journey begins. Watchmakers, engineers, and designers collaborate to create timepieces that are not only aesthetically appealing but also highly functional. The design must consider not only the appearance of the watch but also the precision of its internal movement. Many luxury brands pride themselves on their iconic, often proprietary, designs that have been passed down through generations.
b. Crafting Components
Once the design is finalized, the components are meticulously crafted. Traditional watchmaking utilizes a variety of materials such as stainless steel, gold, and ceramics. Each part, from the tiny gears to the case, is carefully fabricated by hand or using advanced machinery to achieve the precision required. Even in the case of mass-produced watches, the level of detail and effort required in this stage is enormous.
c. Assembly and Finishing
After the components are created, they are assembled with exceptional care. Watchmakers then engage in finishing processes, such as polishing, engraving, and decorating the components, which add both visual appeal and refinement. This step is critical for ensuring the smooth operation of the movement, and it can take weeks or even months to perfect.
d. Quality Control
The final step in the process is rigorous testing and quality control, ensuring that the watch works flawlessly and meets the brand’s high standards. The testing phase is especially important in mechanical watches, as the functionality of the movement must be accurate and reliable.
While the traditional process is highly time-consuming and labor-intensive, it results in a product that is often regarded as a work of art—something that reflects the skill and dedication of the watchmaker.
2. 3D Printing: The Basics and Its Impact on Manufacturing
3D printing, also known as additive manufacturing, is a process where material is deposited layer by layer to build a three-dimensional object based on a digital model. Unlike traditional manufacturing methods such as milling or casting, 3D printing does not require molds or tooling, which allows for greater flexibility in design and production.
In the context of watchmaking, 3D printing has the potential to significantly alter the way watches are created. The technology allows watchmakers to create complex geometries and shapes that would be difficult, if not impossible, to achieve with traditional methods. Additionally, 3D printing can be used to prototype new designs quickly, reduce production costs, and increase customization options for customers.
3. Advantages of 3D Printing in Watchmaking
a. Complex Designs and Customization
One of the most exciting aspects of 3D printing is its ability to create highly intricate and complex designs. The precision of 3D printers allows for the creation of parts with geometries that were previously unattainable. Watchmakers can use 3D printing to experiment with new designs, produce components with fine details, and even manufacture intricate movement parts that would be challenging to produce by hand.
In addition to design flexibility, 3D printing offers the potential for greater customization. Consumers could potentially have the opportunity to personalize the components of their watches, creating one-of-a-kind pieces tailored to their preferences. This level of customization could be especially appealing in the luxury watch market, where exclusivity and individuality are highly valued.
b. Rapid Prototyping and Iteration
In traditional watchmaking, the process of creating prototypes and iterating on designs can be time-consuming and costly. Watchmakers often rely on trial and error, producing multiple prototypes to test different designs. 3D printing allows for rapid prototyping, enabling designers to quickly produce a model of a part or an entire watch to evaluate its function and aesthetics. This faster feedback loop can lead to more efficient design iterations and innovation.
With 3D printing, it is possible to produce a prototype within hours, rather than weeks or months. This dramatically shortens the development cycle, helping companies bring new designs to market more quickly. For small-batch or limited-edition watches, this could also reduce the time needed for production.
c. Cost-Effective Manufacturing for Small Runs
Traditional watchmaking requires significant investment in tools and molds, especially when manufacturing limited-run or custom pieces. 3D printing removes many of these barriers, as it does not require costly tooling and molds. For smaller, more limited productions or one-off pieces, this can significantly reduce production costs, making it more feasible for independent watchmakers or boutique brands to create high-quality timepieces.
Additionally, the reduction in material waste—due to the additive nature of 3D printing—can lead to a more sustainable approach to manufacturing. Watchmakers can produce only the parts they need, minimizing the environmental impact associated with traditional methods, which often generate considerable waste.
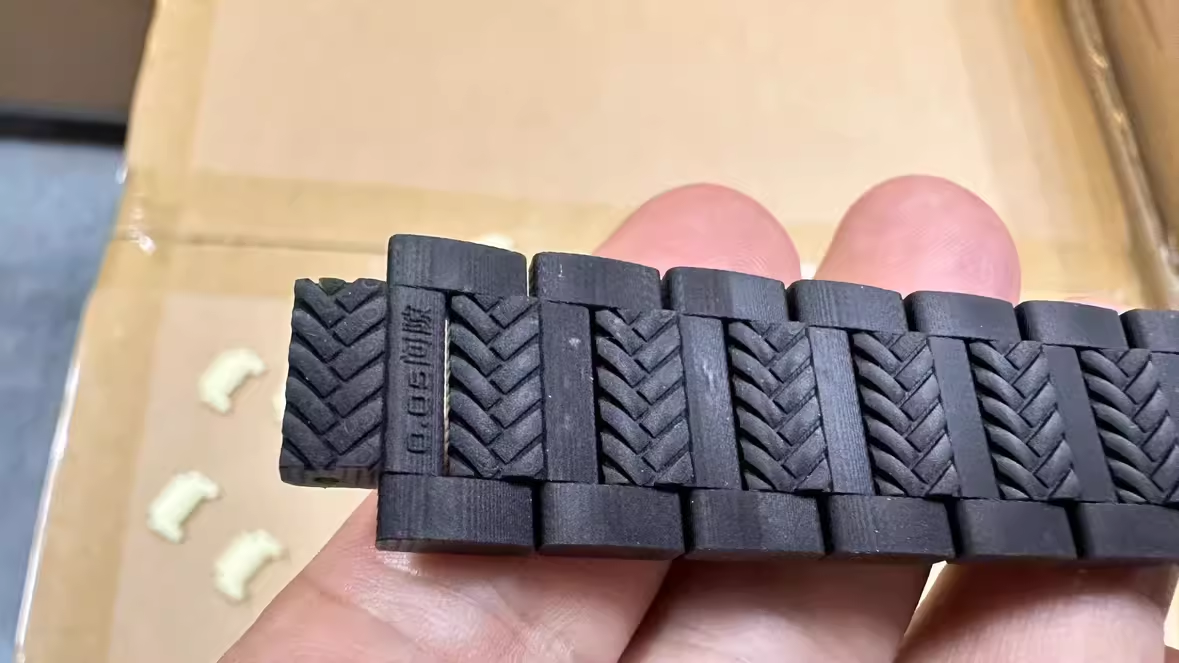
4. Challenges of 3D Printing in Watchmaking
Despite its potential, 3D printing faces several challenges that could hinder its widespread adoption in the traditional watchmaking industry.
a. Material Limitations
While 3D printing technology has advanced significantly in recent years, there are still limitations when it comes to the types of materials that can be used. While metals like titanium and stainless steel can be 3D printed, the quality of the printed metal is often not as high as those created through traditional forging or milling processes. The texture, finish, and strength of the materials produced by 3D printing can also fall short when compared to those crafted through traditional methods.
Luxury watch brands are highly particular about the materials used in their timepieces, as the feel, weight, and durability of a watch are essential to its prestige and value. Until 3D printing can offer materials that meet these high standards, it may be limited in its use for premium and high-end timepieces.
b. Finishing and Aesthetic Quality
While 3D printing offers incredible precision, the surface quality of 3D printed parts may not always match the smoothness and finishing of traditionally manufactured components. Mechanical watches often require fine polishing, engraving, and other detailed finishing work that can take days or weeks to perfect. While 3D printing is improving in this area, it is still a challenge to replicate the hand-finishing techniques that are critical to the look and feel of luxury watches.
For high-end brands, the final aesthetic appeal of the watch is just as important as its technical performance. Until 3D printing can deliver a level of finish comparable to traditional handcrafting, its use in the luxury watch sector may be limited.
c. Integration with Traditional Movements
Mechanical movements, which power many luxury watches, are highly complex and require precise engineering to ensure accuracy and durability. While 3D printing can be used to manufacture parts of the watch case and bracelet, the internal movement is far more challenging. Creating components for the movement, such as gears, springs, and escapements, requires extremely tight tolerances and exceptional material properties.
Incorporating 3D printing into the movement itself may be a significant hurdle, as the materials used in the movement must be durable, wear-resistant, and capable of withstanding significant stress. Until 3D printing can consistently deliver components of the same caliber as traditional methods, it may be limited to non-critical parts like watch cases, dials, and bracelets.
5. The Future of 3D Printing in Watchmaking
While 3D printing technology has the potential to revolutionize certain aspects of watchmaking, it is unlikely to completely replace traditional methods anytime soon, particularly in the realm of luxury mechanical timepieces. However, its ability to enhance the design, prototyping, and manufacturing process can offer significant benefits to the industry.
In the coming years, we may see 3D printing becoming an increasingly valuable tool for independent watchmakers, boutique brands, and even established luxury houses looking to experiment with new designs and limited editions. As material science and printing techniques continue to improve, it is likely that 3D printing will play an even greater role in the future of watchmaking, particularly in more accessible, high-tech timepieces.
Ultimately, 3D printing is likely to be seen as a complementary technology that can enhance traditional watchmaking, rather than a full-fledged replacement for the craftsmanship, artistry, and legacy that define classic horology.
6. Conclusion
3D printing technology has certainly shown its potential to innovate the watchmaking process, offering new opportunities for customization, design, and cost-effective manufacturing. However, the technology is not without its challenges, particularly in terms of material quality, finishing, and integration with traditional movements. While it may not yet rival the craftsmanship of classic watchmaking, 3D printing represents an exciting new frontier that will continue to shape the future of horology.
For now, the true revolution lies not in replacing the centuries-old traditions of watchmaking, but in leveraging new technologies to complement and enhance them, ultimately providing a fusion of old-world craftsmanship and modern innovation. As 3D printing evolves, it is likely to play an increasingly important role in the creation of watches that are both beautiful and technically advanced, bringing the future of timekeeping closer than ever before.