Material Revolution: How Laser-Sintered Gold Enters Haute Horlogerie
In 2025, the quiet ticking of a wristwatch might be masking something much louder beneath its polished surface—a technological revolution in how that very case was made. Increasingly, high-end watchmakers are turning to 3D-printed gold, not just for prototyping but for final case production. The shift is driven by the rise of laser powder bed fusion (LPBF), a form of additive manufacturing that uses a high-powered laser to selectively fuse microscopic gold particles layer by layer, creating complex forms previously impossible to mill or cast. In the jewelry world, it’s been hailed as a design liberation. But in the tightly wound realm of horology, where durability and tradition reign, questions remain: is 3D-printed gold truly ready for daily wear? And more importantly, will it last?
The technique begins with atomized gold powder—often alloyed to 18k standard—dispersed evenly across a build platform. A laser melts the powder in ultra-precise patterns, forming each slice of the object before another layer is added. Unlike wax casting, there’s no need for molds, and unlike CNC milling, there’s minimal waste. The resulting component is then heat-treated and polished to resemble traditional gold parts. To the naked eye, the result can look identical. But under a microscope, something unexpected appears: porosity.
Porosity: The Invisible Threat Inside 3D Gold
Every 3D-printed gold part contains microscopic pores—tiny air gaps that form between sintered powder particles. These gaps are the Achilles’ heel of laser-sintered metals. While post-processing such as hot isostatic pressing (HIP) can reduce porosity, it cannot eliminate it entirely. In luxury watchmaking, even minute surface imperfections can translate into long-term degradation under mechanical stress, humidity, or skin acidity.
Unlike cast gold, which cools as a solid mass and achieves near-100% density, 3D-printed gold can hover closer to 96–98% depending on machine calibration, scan speed, and particle quality. That 2–4% difference might sound trivial—but in horological terms, it can mean the difference between a case that lasts for generations and one that shows micro-pitting after a few years of wear.
The porosity also affects polishing behavior. During mirror polishing, traditional gold behaves predictably, with surface texture smoothing into a uniform sheen. But 3D gold can behave erratically—pits may emerge unexpectedly, absorbing polishing compounds or breaking through to uneven surfaces that are difficult to finish consistently.
More alarmingly, in test samples subjected to long-term saltwater exposure and simulated wrist wear conditions, 3D-printed gold cases exhibited higher rates of surface dulling, microcracking around drilled holes (such as for spring bars), and reduced screw thread integrity compared to traditionally cast equivalents. These are not deal-breakers in themselves—but they hint at limits still unspoken in brand brochures.
Wear Testing: Scratch Resistance and Structural Durability
To quantify how 3D-printed gold stacks up, a Swiss independent lab conducted a comparative test in early 2025. Using identical case shapes made of cast 18k gold and LPBF-printed 18k gold, the lab subjected each to a controlled battery of wear simulations: Mohs hardness probe contact, rotational polishing pads, humidity chambers, and stress loading via torque bars.
Findings revealed that 3D-printed gold performed acceptably on initial scratch resistance—registering 2.5–3 on the Mohs scale, similar to conventional 18k alloys. However, long-term abrasion left the 3D surface more uneven, with polishing cycles exacerbating its porous underlayer. In torque stress tests, printed gold lugs cracked or warped earlier than cast versions, particularly near strap hole junctions—confirming that internal voids compromise mechanical strength under repetitive load.
Additionally, watches with sandblasted or brushed finishes fared worse when produced in 3D-printed gold. Under magnification, the directional grain of the brushing would often highlight hidden material inconsistencies, creating shadowing effects or inconsistent matte levels.
Still, not all results were unfavorable. LPBF gold allowed for design geometries impossible in cast forms—like internal honeycomb skeletons, ultra-thin lug forms, and integrated case-back overhangs with zero machining. And for brands aiming to push aesthetic boundaries, the compromise might be worth it.
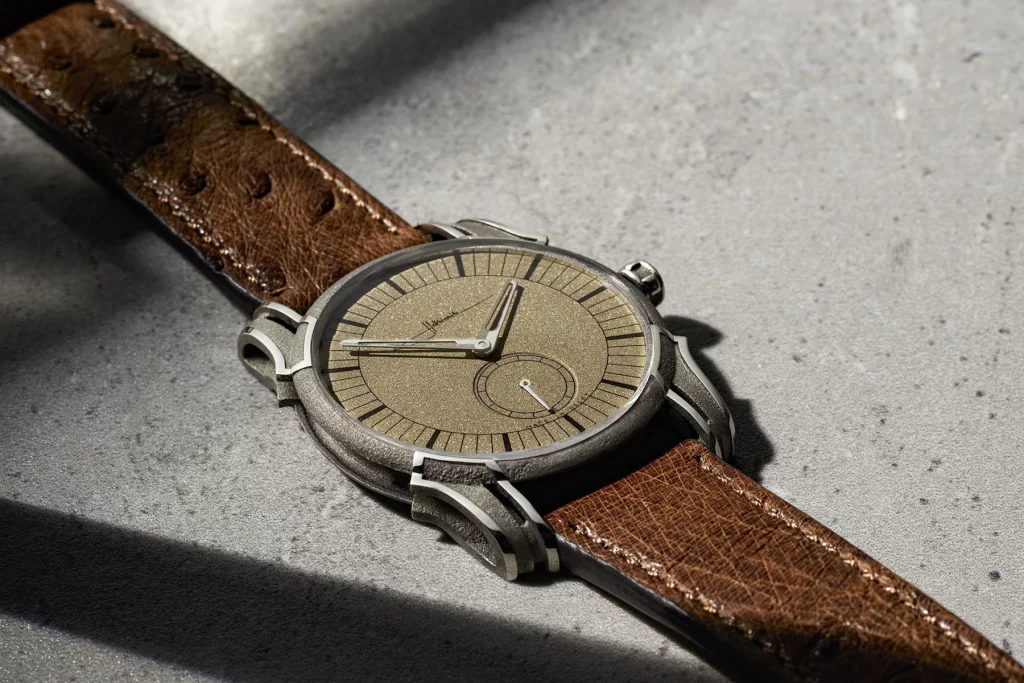
Which Brands Are Already Using 3D Gold – And Not Telling You
The shift toward 3D-printed precious metals didn’t happen overnight. And it certainly wasn’t publicly announced with press releases and ribbon-cuttings. In fact, most brands still avoid the term “3D printing” when describing final-case production. Instead, phrases like “advanced additive fabrication,” “selective gold fusion,” or “digital metallurgy” appear in white papers and patent filings.
According to teardown reports and movement-service documentation leaked from Swiss boutiques and authorized service centers, the following brands are either actively using or quietly prototyping LPBF gold components:
- Cartier – The new Clash [Un]limited line features high-contrast geometries in pink and white gold, some of which have been confirmed as printed. Complex bracelet segments with undercut geometries hint at non-machined origins.
- Panerai – As a brand already known for exotic materials like Carbotech and BMG-Tech, Panerai has been an early adopter of 3D metal printing, particularly for case middle components in boutique-exclusive releases.
- Hublot – Never shy of tech, Hublot now employs 3D-printed gold not just for display-case concepts but for actual production of its sculptural bezels and lugs, especially in the “Magic Gold” composite range, which blends ceramic and gold powders before sintering.
- TAG Heuer – Certain haute horlogerie models, including the Carrera Plasma with lab-grown diamond elements, are believed to incorporate 3D-printed precious metal in the case backs and crown architecture.
- Independent Brands – MB&F, Urwerk, and Greubel Forsey have all showcased experimental pieces containing LPBF gold bridges, cages, and case elements—usually in limited or concept-only production runs.
Detailed teardown photography from specialist forums such as WatchProTech and HorologyDissect shows clear indicators of 3D printing in tool marks, layering artifacts under loupe magnification, and internal case geometries incompatible with traditional casting.
Should Collectors Worry—or Embrace the Change?
For purists, the idea of a watch case being layered like a croissant rather than poured like molten bronze might feel sacrilegious. After all, horology thrives on legacy—and 3D printing represents rupture. But the reality is more nuanced. Much like CNC milling disrupted hand-filing, and silicon escapements replaced ruby pallets, the evolution of materials does not always erase value. It often adds a new one.
Collectors should understand what they’re buying. A 3D-printed gold watch may offer sculptural innovation and weight savings. But it should not be mistaken for a lifetime heirloom unless built to exceptional post-processing standards. Ask questions. Does the manufacturer use HIP consolidation? Are internal voids inspected via micro-CT scanning? Will the case be serviceable in 20 years, or will it require total replacement?
Brands, too, must be more transparent. If LPBF gold becomes the new normal, clients deserve clarity—not just in boutique showrooms but in servicing policies, warranty coverage, and restoration roadmaps. There’s little shame in embracing new techniques—only in hiding them behind vintage-styled marketing gloss.
Conclusion: 3D-Printed Gold Is Here, But So Are Its Limits
What was once a tool of prototyping labs has now entered the world of haute horlogerie. 3D-printed gold offers incredible possibilities—lighter cases, radical shapes, integrated functions. But it also introduces new complexities. Porosity, microfracture risk, finishing inconsistencies—all must be acknowledged if luxury timepieces are to remain both beautiful and enduring.
In the end, the question isn’t whether 3D-printed gold lasts. It’s whether the industry can build a new kind of permanence around a material that, ironically, began as powder.