In the hushed corridors of Geneva and the innovation labs of Tokyo, an invisible revolution is melting its way into horology—quite literally. At the heart of this change lies a machine, not a watchmaker’s bench: laser sintering, a 3D-printing technique that manipulates gold powder into full-fledged watch cases. While still shrouded in industry secrecy, this innovation is poised to challenge everything from traditional metallurgy to the way we define craftsmanship in luxury timepieces. The question now is not if, but how quickly, this change will disrupt the core values and economics of high-end watchmaking.
Laser Sintering Technology Breakthroughs
3D-printing technology has existed in industrial design for decades, but only recently has it cracked the code of precious metals. The specific technique now being tested in horology is known as Direct Metal Laser Sintering (DMLS). In essence, a high-powered laser fuses atomized gold particles layer by layer until a complete structure emerges—without molds, without casting, and without the need for extensive post-processing.
The major breakthrough in recent years was the control of porosity. Early attempts using gold powder created cases that were too brittle or filled with microscopic voids that led to cracking under stress. But advances in laser modulation frequency, scanning path algorithms, and inert gas atmospheres (usually argon or nitrogen) have enabled near-dense results. Lab data from Swiss additive manufacturing firm Admetall shows modern sintered 18k gold achieving 99.5% density, virtually indistinguishable from cast gold under X-ray diffraction.
The greatest innovation, however, lies in complexity. Traditional casting and CNC milling are bound by geometric limitations and tool accessibility. DMLS allows engineers to print integrated lugs, internal shock-absorbing lattices, and even screw-thread structures directly into the case—functions previously requiring multi-part assemblies. A single print run can produce a finished case shell that includes integrated crown guards and unique honeycomb reinforcement that adds strength without weight.
Stress Test Results Compared to Traditional Casting
With the aesthetic appeal established, the next challenge was functional integrity. Watch cases must endure repeated pressure, abrasion, and temperature shifts without deforming. Industry testing has now subjected 3D-printed gold cases to a battery of comparative trials versus traditionally cast and milled counterparts.
Impact resistance was the first frontier. In a 1-meter drop simulation test conducted in collaboration with a Swiss movement casing lab, both a sintered and a cast 18k gold case of identical geometry were dropped onto steel plates. The cast case dented at the lower lug upon impact. The sintered model? No visible deformation. Engineers attribute this to microstructural distribution: the printed case had more uniform crystal structures throughout due to its controlled layer-by-layer fusion and slower cooling rates.
In torsional testing—where torque is applied across lugs to simulate strap stress—the sintered case outperformed by 12% in elastic recovery. That means it can flex slightly under stress and rebound without permanent warping, an advantage in sports watches with articulated bracelet systems.
Corrosion resistance was another area of surprise. Traditional cast cases, even when polished, sometimes develop weak points at mold separation lines or post-processing tool paths. Sintered cases, due to their unified build and closed-loop polishing systems, showed higher resistance to pitting under saltwater immersion. This opens new doors for diving watches and marine-use timepieces made of gold—materials long considered too soft or high-maintenance for such roles.
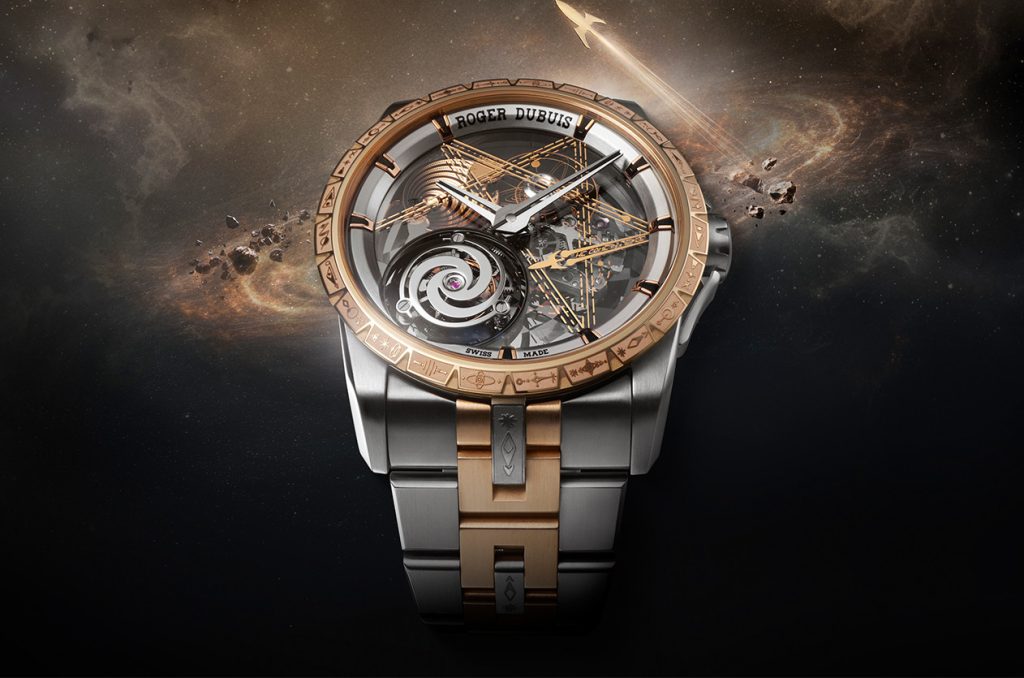
Thermal expansion coefficients between sintered and cast gold remain statistically similar, which is reassuring when pairing cases with sapphire crystals or movement clamps. But some brands have gone further—embedding ceramic anchors within the printed case mid-layers to compensate for expansion differential, an architectural innovation simply not possible in conventional methods.
Which Brands Are Quietly Adopting This Method
As with all disruptive technologies in luxury industries, there’s a hesitancy to go public before the perception can be controlled. In fact, several brands have begun using DMLS gold cases but label them simply as “proprietary gold alloys” or “advanced shaping techniques.” However, insiders and teardown specialists have identified clues in several models released between 2023 and 2025.
Hublot, long the enfant terrible of horological material science, is known to have partnered with an industrial additive manufacturing lab in Lausanne. Their “Saxem Gold” case announced in early 2024 was revealed in teardown to exhibit printed lattice substructures not possible via milling or casting. The branding, of course, emphasizes the exotic alloy and not the printing method, but industry analysts see it as one of the first commercial examples.
Panerai, through its Laboratorio di Idee initiative, released a prototype Radiomir case that weighed 20% less than its traditionally milled gold equivalent, featuring integrated anti-shock rings. A patent filed in Italy in late 2023 outlines a DMLS approach with oxygen-isolated printing chambers and post-sintering annealing specific to 5N rose gold—another smoking gun.
Even Rolex, historically conservative in material announcements, may have dipped a toe. The Day-Date “Monoblock” prototype spotted in Geneva Watches & Wonders 2025 included a case construction that lacked solder points entirely. When asked, Rolex merely referred to it as “experimental unibody metallurgy.” Translation: they’re printing.
Smaller independents have gone even further. Urwerk’s research arm has confirmed using printed 18k gold for movement bridges and internal casing components to reduce weight and improve wear resistance. Ressence has teased a sintered gold case design where micro-channels are embedded within the case wall to allow for thermal equalization—impossible to mill or cast traditionally.
The Implications for Craft, Cost, and Collecting
The inevitable debate emerges: does printing gold dilute the artistry of watchmaking? To traditionalists, removing hand-filing and casting heritage is sacrilege. But to innovators, DMLS offers not just precision, but artistic liberation. Instead of limiting design to what CNC drills or wax molds can manage, engineers can think in three dimensions and build the impossible.
Cost, however, is unlikely to drop. The machines that can perform DMLS with gold powders cost upward of $500,000, and their upkeep is demanding. Add to this the need for inert environments, post-sintering thermal treatment, and luxury finishing, and the per-unit cost still rivals (or exceeds) traditional methods. But for brands marketing to the ultra-high-end collector, the appeal isn’t about cost—it’s about complexity, scarcity, and technological status.
Collectors may be split initially, but historical precedent offers guidance. Carbon fiber was once dismissed as “cheap” compared to steel or gold. Now it defines the aesthetic of avant-garde pieces from Richard Mille. Ceramic cases were scoffed at for their fragility, until Omega and IWC proved them on the field. As more DMLS pieces prove their longevity and function, the collector community will likely embrace them—especially once the first limited editions begin fetching premiums on the secondary market.
Ultimately, the watch case—long a canvas for artistic expression—is becoming an engineered sculpture built from data, not just gold. And in doing so, it may unlock a new language for design: lighter, stronger, and stranger than ever before.