In an age of rapid technological advancements, it is fascinating that many watchmakers still rely on tools that have been in use for over two centuries. The intricate processes of watchmaking have evolved tremendously over the years, yet many traditional methods and tools persist, proving their lasting value in the creation of timepieces that blend art and engineering. In this article, we will explore the vintage tools that watchmakers continue to use today, examining their irreplaceable qualities and discussing the delicate balance between heritage techniques and modern efficiency.
The Art of Traditional Watchmaking: A Legacy of Precision
Before we dive into the specific tools that have stood the test of time, it is essential to understand the fundamental nature of traditional watchmaking. Watchmaking is an ancient craft with its origins dating back to the 16th century, where the earliest timepieces were crafted by hand using rudimentary tools. Over time, watchmaking evolved from simple mechanical mechanisms to the intricate, multi-functional designs we see today.
Despite the rise of automation and computer-aided design (CAD), the core principles of traditional watchmaking—precision, attention to detail, and craftsmanship—remain unchanged. For centuries, watchmakers have used highly specialized tools to create movements, adjust gears, polish components, and assemble the delicate machinery that powers a timepiece.
While modern technology has streamlined some aspects of production, there are certain tasks that demand the expertise and touch of skilled artisans working with traditional tools. These tools have been passed down through generations, each iteration fine-tuning and perfecting the art of watchmaking.
The Vintage Tools That Have Withstood the Test of Time
Many watchmaking tools have been in use for over 200 years, and their enduring relevance speaks to their precision and effectiveness. Some tools have remained unchanged in their design and function, while others have been modified over time to accommodate the changing needs of watchmakers. Below, we highlight some of the key vintage tools that continue to play a vital role in the creation of high-end timepieces.
1. The Lathe
The lathe is perhaps the most iconic tool in the watchmaker’s arsenal. It is used to shape and refine components such as gears, pinions, and screws. Dating back to the 16th century, the lathe was one of the first tools to mechanize the shaping of parts. While modern CNC (Computer Numerical Control) lathes now exist, traditional manual lathes are still highly valued in the industry for their ability to offer unparalleled control and precision when it comes to crafting tiny, intricate components.
What makes the traditional lathe irreplaceable is the personal touch of the watchmaker. With a manual lathe, the artisan can finely adjust the speed, angle, and pressure applied to a piece, achieving a level of precision that is difficult to replicate with automated machines. Many Swiss watchmakers, particularly those in luxury houses like Patek Philippe and Vacheron Constantin, still use manual lathes for certain delicate operations.
2. The Peg Wood
A peg wood, often made from fine-grained wood or occasionally synthetic materials, is used to adjust delicate parts of the movement without damaging the surfaces. Watchmakers use peg woods to manipulate screws, jewels, and other components without leaving marks or scratches. This humble tool has been a staple of watchmaking for centuries, and its use continues in modern horology due to its unmatched effectiveness.
The peg wood’s simplicity belies its importance. It allows the watchmaker to gently apply pressure on components without the risk of marring delicate surfaces, which could cause malfunction or cosmetic damage. It is a tool that has stood the test of time because of its simple yet essential function.
3. The Bezel Press
The bezel press is used to fit the watch crystal or bezel onto the case. This tool ensures that the components are securely placed, preventing dust, moisture, and other external elements from entering the watch. The design of the bezel press has remained relatively unchanged over the years, as it provides the level of control and precision necessary for properly sealing the case.
For many watchmakers, the bezel press is considered an indispensable tool in the assembly process. The gentle force it applies ensures that the bezel is aligned perfectly with the case, preventing any unwanted gaps or misalignments. While more modern tools exist, the bezel press is still revered for its reliability and effectiveness.
4. The Poising Tool
A poising tool is used to balance the wheel and escapement of the movement to ensure that the watch keeps accurate time. Precision in this step is essential, as even the slightest imbalance can cause the timepiece to run inaccurately. Traditionally, this tool is used by hand, allowing watchmakers to make small adjustments with the utmost care.
The poising tool’s effectiveness lies in its precision and ability to adjust the delicate parts of the movement without causing any damage. Despite the advances in technology, many high-end watchmakers still prefer to use this manual tool for critical adjustments, as it allows for finer, more customized tweaking than automated processes.
5. The Screwdriver Set
Watchmakers use specialized screwdrivers to adjust or tighten the screws in a timepiece. These tools are made with incredibly thin, precise tips that allow watchmakers to work on tiny screws without damaging the surrounding components. The screwdriver set, with its range of sizes, allows for flexibility and precision when handling the small screws that are used in the assembly of a watch.
While modern screwdrivers have been improved with materials like stainless steel and tungsten, the traditional craftsmanship and care that go into using these tools have remained largely the same. Watchmakers continue to value their reliability and precision, as these tools allow for intricate adjustments without compromising the integrity of the watch.
The Balance Between Tradition and Modern Efficiency
While traditional tools like the lathe, peg wood, and screwdriver set remain essential to high-end watchmaking, it is important to understand the role of modern efficiency in the industry. Watchmaking has evolved, and many modern tools and machines have streamlined the production process, increasing both speed and accuracy.
For example, CNC machines have revolutionized the production of small parts, reducing the time and labor required for component shaping. Similarly, laser engraving and 3D printing technologies have allowed for rapid prototyping and precision manufacturing. These modern tools are especially useful for mass production and the creation of certain components that require consistent and repeatable results.
However, despite the clear advantages of these new tools, they cannot entirely replace the craftsmanship and artistry associated with traditional watchmaking. The most prestigious watchmakers in the world continue to rely on traditional methods to ensure the highest quality. Many luxury brands use a hybrid approach, combining traditional craftsmanship with modern tools to maintain both heritage and efficiency.
For example, while modern CNC lathes may be used for the bulk of the production, watchmakers often turn to manual lathes for delicate finishing work. Similarly, digital technologies like laser calibration may help with testing and quality control, but the final assembly and adjustments are still done by hand using the same tools that have been used for centuries.
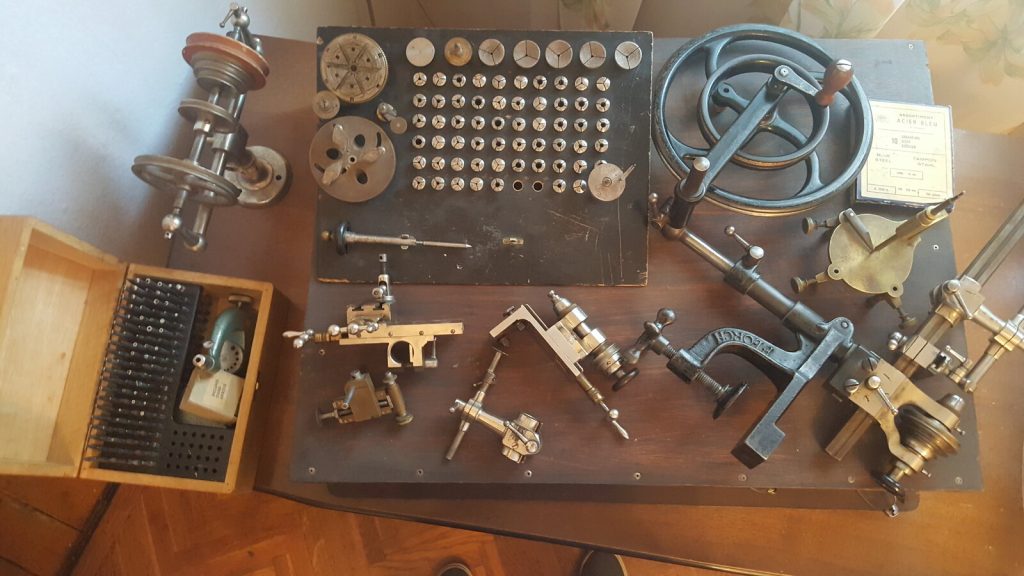
Why These Tools Are Irreplaceable
The enduring appeal of traditional tools in the world of horology lies in their ability to provide a level of control and craftsmanship that modern machines cannot replicate. Here are a few reasons why these tools remain irreplaceable:
1. Precision and Control
Traditional tools offer an unparalleled level of precision and control that is often difficult to achieve with modern machines. The hands-on nature of manual tools allows watchmakers to make small, nuanced adjustments that can drastically affect the functionality and appearance of a timepiece.
2. Artistry and Craftsmanship
Watchmaking is as much an art as it is a science. The skill and artistry that come with using traditional tools are essential for creating timepieces that are not only functional but beautiful. The subtle finishing touches applied by hand can make all the difference between a mass-produced timepiece and a masterpiece.
3. Heritage and Legacy
For many watchmakers, the tools they use are part of a rich legacy that has been passed down through generations. By using traditional tools, they are not only creating a timepiece but preserving a piece of horological history. There is a deep sense of pride in maintaining these traditions and continuing a legacy of craftsmanship that has been honed over centuries.
4. Emotional Connection
There is an emotional connection between the watchmaker and the tools they use. Traditional tools are often finely crafted and have a unique character that modern machines lack. Many watchmakers feel that using these tools connects them to the history and legacy of their craft, enhancing the satisfaction they get from the work they do.
The Future of Watchmaking: A Blend of Old and New
As we look toward the future of watchmaking, it is clear that traditional tools will continue to play an integral role in the craft. While the tools of the trade may evolve with the advent of new technologies, the core principles of precision, artistry, and heritage will remain unchanged. Watchmakers will continue to blend heritage techniques with modern innovations, creating timepieces that honor the past while embracing the future.
The fascinating balance between traditional craftsmanship and modern efficiency is what makes the world of horology so unique. Whether working with 200-year-old tools or the latest technological advancements, the pursuit of perfection and timeless elegance will always be at the heart of watchmaking.