The world of watchmaking, traditionally known for its meticulous craftsmanship and intricate mechanical movements, has been undergoing a significant transformation. At the forefront of this revolution is 3D printing and additive manufacturing—technologies that allow for the creation of watch components with unparalleled precision and flexibility. In this article, we will explore how these cutting-edge technologies are revolutionizing watch design and production processes, and their impact on the industry at large.
The Basics of 3D Printing and Additive Manufacturing
Before diving into the specific ways 3D printing is reshaping the watch industry, it is essential to understand the fundamentals of 3D printing and additive manufacturing.
3D printing, also known as additive manufacturing, involves creating objects by adding material layer by layer, based on a digital 3D model. This is in contrast to traditional manufacturing methods, which often involve subtracting material from a larger block (such as milling or cutting). The precision and versatility of 3D printing make it an attractive option for industries requiring high levels of detail and customization—such as the watchmaking world.
The process involves a variety of technologies, including stereolithography (SLA), selective laser sintering (SLS), and fused deposition modeling (FDM), each of which has unique advantages. In the context of watchmaking, the most commonly used methods are SLA for detailed designs and SLS for functional parts that require strength and durability.
3D Printing in Watch Design: Creative Freedom and Customization
One of the most significant benefits of 3D printing is its ability to enable unlimited creativity in watch design. Designers can now create complex geometries and intricate details that were previously impossible to achieve with traditional methods. This has opened the door for avant-garde designs and unconventional materials, allowing watchmakers to push the boundaries of aesthetics and functionality.
Freedom of Design
With 3D printing, watchmakers no longer need to rely on traditional methods like stamping or casting to create complex shapes. Intricate patterns, organic forms, and complex curves can now be designed with ease, offering far more design flexibility. This has led to the rise of experimental and artistic watches, where geometrical shapes, fine textures, and unique finishes come together in bold new ways.
For example, famous Swiss watchmakers have begun utilizing 3D printing to create intricate cases, complicated dials, and customized components that would have been too challenging or costly to produce using traditional methods.
Personalized Watches
Another significant impact of 3D printing is its ability to facilitate personalized watchmaking. Consumers now have the opportunity to design their own custom timepieces, selecting everything from the case shape to the dial design and even the material composition. This opens up new possibilities for bespoke watches, where each piece is uniquely crafted to reflect the wearer’s personal taste and style.
Brands like MB&F and Bulgari have already started using 3D printing to create unique, one-of-a-kind pieces for high-net-worth individuals, demonstrating the immense potential for personalization in luxury watchmaking.
Streamlining Production: Faster, More Efficient Manufacturing
Beyond the realm of design, 3D printing is also revolutionizing the production process of watches. Traditional watchmaking often involves labor-intensive processes, with parts that are carefully hand-finished and assembled. In contrast, 3D printing allows for rapid prototyping and production scaling with far fewer steps and lower costs.
Prototyping and Design Testing
For watchmakers, one of the most significant advantages of 3D printing is the ability to create rapid prototypes. Designers can now quickly produce prototypes of watch cases, straps, and internal components in a matter of hours, instead of weeks. This rapid turnaround allows for faster design iterations and more extensive testing before production begins, ultimately resulting in better-designed watches.
Additionally, additive manufacturing allows watchmakers to test different materials and finishes for components, helping them choose the optimal option for each part of the watch. Whether it’s testing metal alloys, ceramics, or even titanium, 3D printing gives manufacturers the flexibility to experiment with new materials that enhance the performance and aesthetics of their timepieces.
Efficiency in Mass Production
While 3D printing was once considered a tool for prototyping or one-off custom pieces, it is now being utilized for small-scale mass production in the watch industry. Using additive manufacturing technologies, manufacturers can streamline production by directly printing parts like case backs, bracelets, or even movement components without the need for complex tooling or molds.
This reduction in production time and cost is especially valuable for smaller independent brands that may not have the resources for traditional mass production methods. In this way, 3D printing is democratizing the watchmaking industry, allowing smaller, independent watchmakers to compete with established luxury brands.
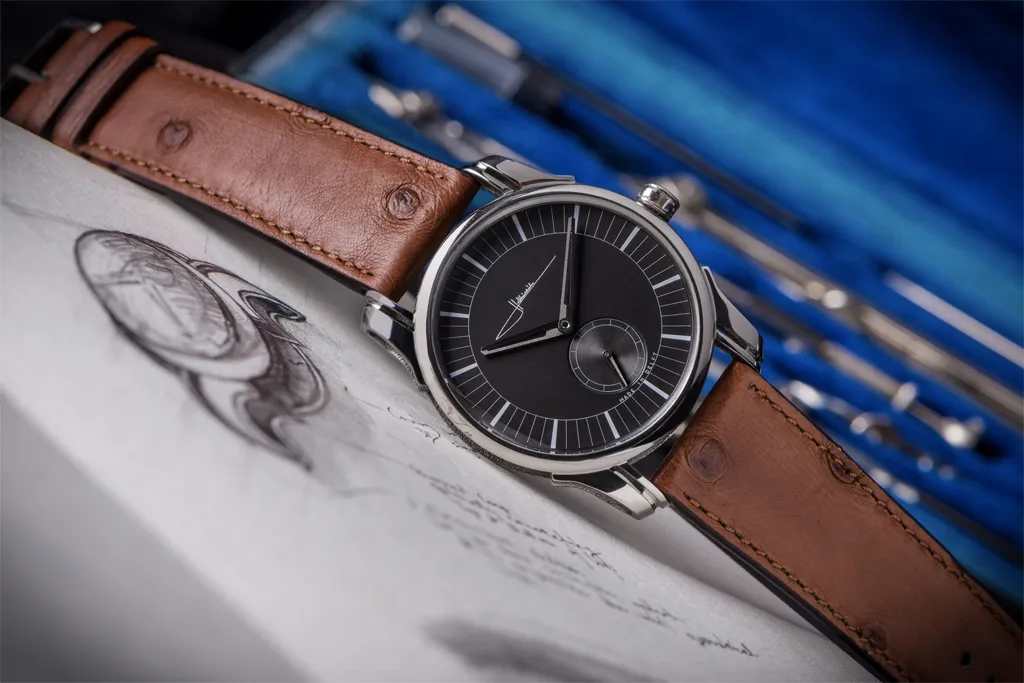
Materials Innovation: New Possibilities for Watch Components
In addition to enabling innovative designs and faster production, 3D printing has also opened the door for new materials to be used in watchmaking. Traditional materials like stainless steel, gold, and ceramics remain staples in the industry, but 3D printing allows watchmakers to experiment with exotic materials that were previously difficult to process.
Metal 3D Printing
One of the most exciting developments in 3D printing for watchmaking is the ability to print with metal. While metal 3D printing has been around for some time, recent advancements have made it more accessible and affordable for the luxury watch industry. Watchmakers are now able to create metal cases, movement parts, and other intricate components using titanium, gold, and platinum through 3D printing, enabling new levels of customization and durability.
For example, Bulgari has used 3D-printed titanium to create ultra-lightweight, high-performance watches, combining both innovative design and cutting-edge materials.
Polymer and Resin Materials
3D printing with polymers and resins is also a key area of development, particularly for watch cases and straps. These materials are often more flexible and versatile than metals and can be used to create lightweight components with high strength-to-weight ratios. Carbon fiber, nylon, and resin composites are some of the materials that can be printed for parts like bracelets and cases, offering durability, comfort, and a modern look.
Challenges and Limitations of 3D Printing in Watchmaking
While 3D printing has revolutionized many aspects of watchmaking, there are still limitations that must be considered. For example, 3D-printed metal parts can sometimes lack the same level of finish or polish that is achieved through traditional methods like casting or machining. Additionally, material limitations can restrict the types of components that can be effectively printed. For example, while stainless steel and titanium can be 3D printed, precious metals like 18k gold or platinum are more difficult to work with due to their properties.
Furthermore, while 3D printing enables innovation, it also poses a challenge for traditional watchmakers who must adapt to new manufacturing processes. This shift toward digital fabrication requires specialized knowledge and expertise, and the cost of implementing 3D printing technologies can be significant, particularly for smaller brands.
The Future of 3D Printing in Watchmaking
Looking ahead, it’s clear that 3D printing will continue to play a major role in the evolution of watchmaking. As the technology advances, it is expected to make customization more accessible, accelerate innovation, and create new opportunities for brands to experiment with materials and designs. The ability to create highly personalized, intricate, and functional timepieces with speed and precision will undoubtedly continue to drive the growth of 3D-printed watches.
Sustainability in Watchmaking
One of the most exciting future possibilities for 3D printing in watchmaking is its potential to contribute to sustainability. As the industry becomes more aware of the environmental impact of manufacturing, 3D printing can help reduce material waste, as the process only uses the exact amount of material needed to produce each component. Additionally, the ability to use recycled materials and eco-friendly resins in 3D printing will allow brands to produce watches with a smaller environmental footprint.
Conclusion: A New Era of Watchmaking
The intersection of 3D printing and watchmaking marks the beginning of a new era in the industry, one where design, customization, and manufacturing processes are being redefined. By allowing for unmatched creativity, speed, and efficiency, 3D printing technologies are changing the way watches are designed, produced, and even worn. While challenges remain, the potential for this revolutionary technology to enhance both the artistic and technical aspects of watchmaking is enormous. The future of the industry is bound to be shaped by these innovations, paving the way for new, exciting possibilities in the world of horology.