Introduction: The Intersection of Tradition and Innovation
The watchmaking industry has long been known for its meticulous craftsmanship, centuries-old techniques, and unwavering commitment to precision. Traditional watchmakers take pride in hand-finishing components, assembling movements with the utmost care, and creating timepieces that stand as symbols of both art and technology. However, in recent years, a new technological advancement has begun to make waves in various industries, and that innovation is 3D printing.
While 3D printing, also known as additive manufacturing, has already disrupted numerous fields—including aerospace, automotive, and medical industries—its impact on the world of horology (the art and science of watchmaking) is still a topic of much debate. Will it completely change the way watches are made, or will it remain a niche tool for certain components?
In this article, we’ll explore the pros and cons of 3D printing in watchmaking, analyzing its potential to transform the industry while considering its effects on craftsmanship, quality control, and affordability. We will dive into how 3D printing could open up new possibilities for watch design and manufacturing, as well as examine the challenges and limitations it faces in a world where tradition often reigns supreme.
3D Printing and Watchmaking: The Basics of Additive Manufacturing
How 3D Printing Works in Watchmaking
3D printing, or additive manufacturing, is the process of creating three-dimensional objects from a digital design by laying down successive layers of material. The technique contrasts with traditional manufacturing methods such as machining, which involves cutting away material from a solid block, or casting, which requires creating a mold.
In watchmaking, 3D printing allows for the creation of complex geometries and intricate designs that would be nearly impossible or highly time-consuming to produce using traditional methods. The ability to print custom watch components with extreme precision opens up a world of possibilities for designers and engineers looking to push the boundaries of traditional watchmaking.
Materials Used in 3D Printing Watches
One of the significant advantages of 3D printing is its versatility in terms of materials. In watchmaking, a range of materials can be used for additive manufacturing, including:
- Metals: Precious metals like gold, silver, and platinum can be 3D printed, as well as more industrial materials like titanium and stainless steel.
- Plastics: High-performance plastics like resin and nylon are used for prototype parts and low-cost components, such as watch casings or straps.
- Ceramics: Some watch brands have even begun experimenting with ceramic 3D printing, which can offer sleek and durable materials for creating cases and bezels.
- Composite Materials: High-end watchmakers have also explored using carbon fiber and other composites for ultra-lightweight and high-strength components.
As technology advances, more materials are becoming available for 3D printing, allowing watchmakers to experiment with new textures, colors, and finishes that weren’t possible with traditional manufacturing techniques.
The Advantages of 3D Printing in Watchmaking
1. Enhanced Customization and Design Flexibility
One of the most exciting aspects of 3D printing in watchmaking is the potential for greater customization. Traditional watch manufacturing often requires expensive molds and tooling for mass production, making it challenging to create unique or limited-edition designs. With 3D printing, watchmakers can easily customize designs or create one-off pieces tailored to the preferences of individual customers.
- Intricate Designs: 3D printing allows for the creation of incredibly intricate designs with organic shapes and geometries that would be impossible to achieve with conventional machining or casting.
- Bespoke Watches: Watch brands can offer bespoke timepieces with personalized engravings, customized features, and unique shapes, thus appealing to an exclusive market that values individuality.
This capability is a game-changer for high-end brands and independent watchmakers who want to offer tailored luxury and distinctive products that stand out from mass-produced watches.
2. Reducing Manufacturing Costs and Lead Times
Traditional watchmaking methods often require significant labor and time investment. Creating individual components for a watch—especially for custom models—can be expensive and time-consuming. With 3D printing, watchmakers can streamline the manufacturing process, reduce production costs, and speed up the production timeline.
- Prototyping: Instead of spending weeks or months on producing prototypes through traditional methods, designers can use 3D printing to rapidly prototype new designs, make adjustments, and test them in real-time.
- On-Demand Production: 3D printing offers the ability to produce watch components on-demand, reducing waste and inventory costs. This is particularly valuable for producing limited-edition collections or small-batch watches.
For independent watchmakers or smaller companies, the ability to reduce manufacturing costs can make it easier to compete in the competitive luxury watch market.
3. Precision and Quality Control
3D printing can offer remarkable levels of precision that rival traditional manufacturing methods. This is especially important in watchmaking, where even the smallest imperfections can affect the accuracy and reliability of the timepiece.
- Micron-Level Accuracy: Modern 3D printers can achieve incredibly fine resolution, producing components with micron-level accuracy—vital for the tiny, intricate parts found in mechanical watches.
- Consistency: Because 3D printing uses digital blueprints, each component produced is virtually identical, offering consistency in parts that can sometimes be difficult to achieve with manual processes.
In terms of quality control, 3D printing allows for precise inspections and measurements of each component during production. This helps ensure that each piece meets the brand’s standards for both aesthetic and functional quality.
4. Sustainability and Waste Reduction
Traditional manufacturing processes often produce a significant amount of waste, especially when cutting away material from larger blocks to create watch components. In contrast, 3D printing is an additive process, meaning that material is only used where it’s needed, significantly reducing waste.
This sustainability factor has become an increasingly important consideration for both consumers and companies in the watch industry, especially as more brands seek to minimize their environmental impact. By adopting 3D printing, watchmakers can contribute to a greener manufacturing process while still producing high-quality timepieces.
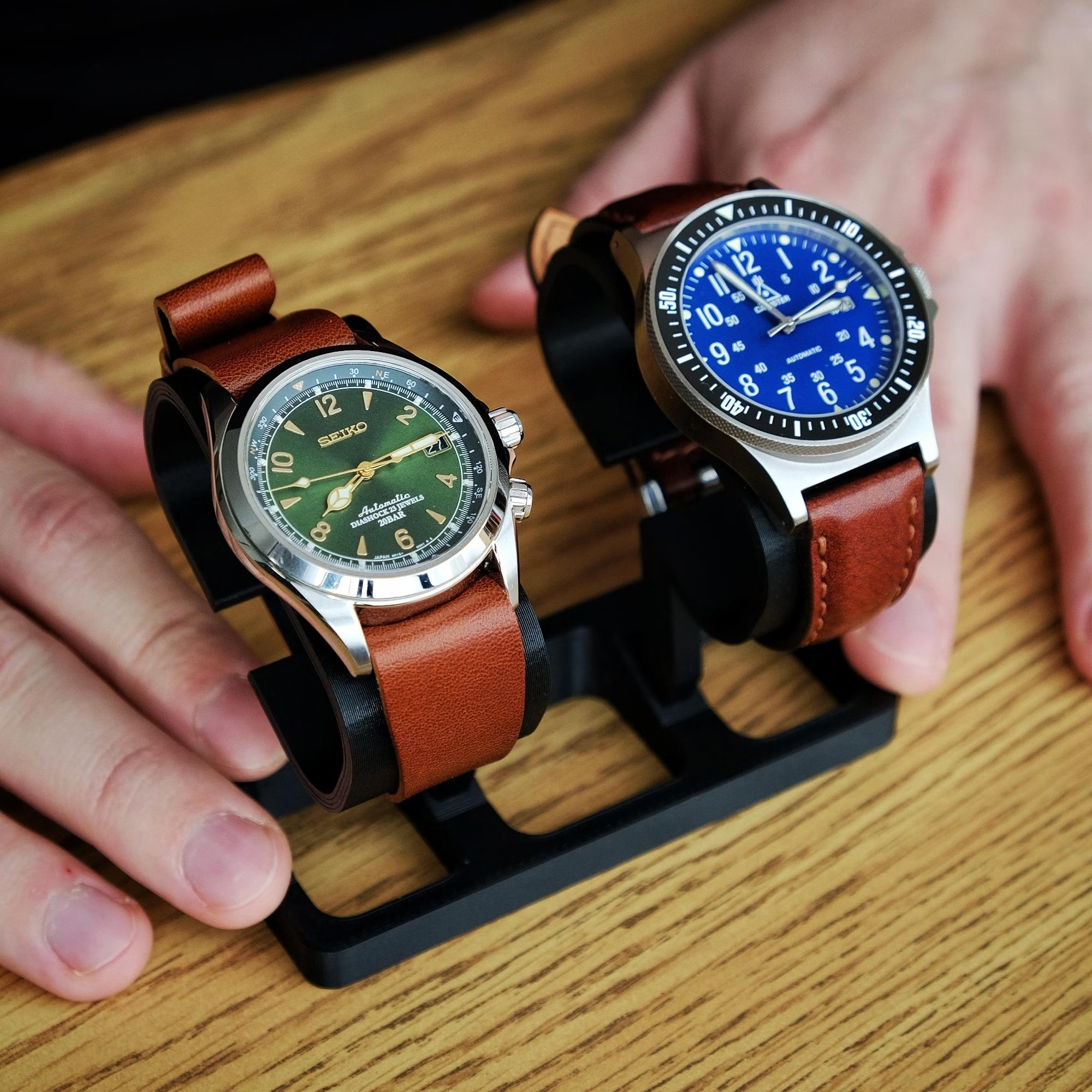
The Challenges of 3D Printing in Watchmaking
1. Material Limitations
While 3D printing offers a wide range of materials, the technology is still not capable of replicating every material traditionally used in watchmaking. Precious metals like gold or platinum can be 3D printed, but the process may not yet achieve the same density or strength as traditional casting methods. Furthermore, there may still be challenges with producing certain materials, like enamel, that are integral to some luxury watches.
- Limited Availability of Materials: Some high-end watchmakers prefer specific materials for certain components, such as 18k gold, high-grade stainless steel, or brazed metals. While 3D printing is advancing rapidly, these materials are still difficult to work with in the context of additive manufacturing.
- Finish and Detail: Some watchmakers are concerned about the finish of 3D printed parts, especially for components that require fine polishing or engraving. While printing can create precision parts, the surface finish may not always meet the standards expected by luxury brands.
2. Craftsmanship and Tradition
While 3D printing offers technological advantages, it also raises questions about the impact on craftsmanship in watchmaking. The fine art of hand-finishing, engraving, and assembling individual components has been a hallmark of watchmaking for centuries. There is a concern that as 3D printing becomes more prevalent, traditional skills and human expertise may be overshadowed by machines.
- Loss of Artisanal Touch: Some purists argue that watchmaking craftsmanship cannot be replicated by machines. The subtle nuances and attention to detail found in hand-finishing components could be lost in a fully automated production process.
- Craft vs. Mass Production: Another concern is that 3D printing could lead to the mass production of watches, undermining the exclusivity and luxury associated with traditional high-end timepieces. The uniqueness of a handmade watch could be diminished if 3D printing becomes commonplace for mass-market models.
3. Durability and Long-Term Performance
Though 3D printing allows for impressive design flexibility, some watchmakers worry about the long-term durability and performance of 3D printed components. Traditional methods, such as machining or casting, have stood the test of time for centuries, proving their ability to produce components that last for generations.
- Longevity: Concerns remain about whether 3D printed components, particularly those made from plastics or composites, can withstand the wear and tear expected of a luxury timepiece.
- Structural Integrity: Some materials used in 3D printing may not offer the same strength or resilience as traditionally produced components. For instance, parts like gears or escapements that require constant movement may be vulnerable to degradation over time.
Conclusion: The Future of 3D Printing in Watchmaking
The introduction of 3D printing into the world of horology presents both exciting opportunities and formidable challenges. On the one hand, it offers a chance to innovate with new materials, create custom designs, and reduce production costs. On the other hand, there are concerns about its impact on craftsmanship, quality, and the luxury appeal of traditional watches.
As technology advances, 3D printing will likely play an increasingly prominent role in the watchmaking process, particularly for prototypes, limited editions, and certain components. However, it is unlikely to completely replace traditional methods in high-end, luxury watchmaking, where craftsmanship and artistry are paramount.
Ultimately, the question is not whether 3D printing will revolutionize watchmaking, but how it will complement and enhance traditional practices. The future may see a harmonious blend of both worlds—combining the innovative power of technology with the timeless craftsmanship that has made watches symbols of both precision and luxury for centuries.