Tracing the Origins: The Japanese “Tatara” Steelmaking and Grand Seiko Cases
In the world of luxury watchmaking, the pursuit of perfection often leads to unexpected intersections between ancient craft and modern technology. One striking example is how Grand Seiko, the revered Japanese watch brand known for its meticulous finishing, draws inspiration from a blacksmithing technique dating back over 400 years — the legendary “Tatara” steelmaking process. This traditional Japanese method, originally developed to create the famed tamahagane steel used in samurai swords, has found new life influencing the finishing and material quality of some of today’s most admired watch cases.
Tatara steelmaking involves smelting iron sand and charcoal inside a clay furnace, producing steel of remarkable purity and toughness. While modern watch case materials and manufacturing often rely on CNC machining and industrial processes, Grand Seiko’s craftsmen integrate the spirit and aesthetic sensibilities of this age-old forging tradition into their finishing techniques. The juxtaposition of centuries-old artistry with cutting-edge precision engineering creates a unique balance between form, function, and cultural heritage rarely seen outside Japan.
Grand Seiko’s famed Zaratsu polishing — renowned for its distortion-free mirror finish — echoes the patience and precision of traditional Japanese metalworking. By channeling the ethos of the Tatara blacksmiths, their artisans achieve not only flawless surface quality but also a depth and resonance that feels almost alive, as if the spirit of the forge remains embedded in every curve of the watch case.
Traditional Forging vs CNC Machining: A Comparative Experiment
In the modern era, the vast majority of luxury watch cases are crafted through CNC (computer numerical control) machining. This automated process allows for incredible precision and repeatability, cutting and shaping metal blocks into complex forms with micrometer accuracy. CNC machining ensures that every case meets stringent dimensional tolerances and consistent quality, essential for mass production and global distribution.
However, while CNC excels in efficiency, it can sometimes fall short in the nuanced aesthetics that elevate a watch case from mere component to object of desire. The surface texture and subtle reflections achieved by a master blacksmith’s hand polishing or forging can imbue the metal with a vibrancy difficult to replicate by machine alone.
To explore this difference, a comparative experiment was conducted between two case finishing methods inspired by Tatara traditions versus modern CNC machining. In this trial, steel cases were first forged and hand-finished by traditional methods involving repeated hammering, annealing, and meticulous polishing with specially selected natural stones. These cases were then compared with counterparts produced entirely by CNC milling and standard machine polishing.
The results were striking. The hand-forged cases displayed a warmer, more organic interplay of light and shadow on their surfaces, a subtle curvature imperceptible to machines but palpable to the eye. The tactile sensation of these finishes also differed—hand-polished cases felt smoother and more inviting to touch, as if inviting a closer inspection.
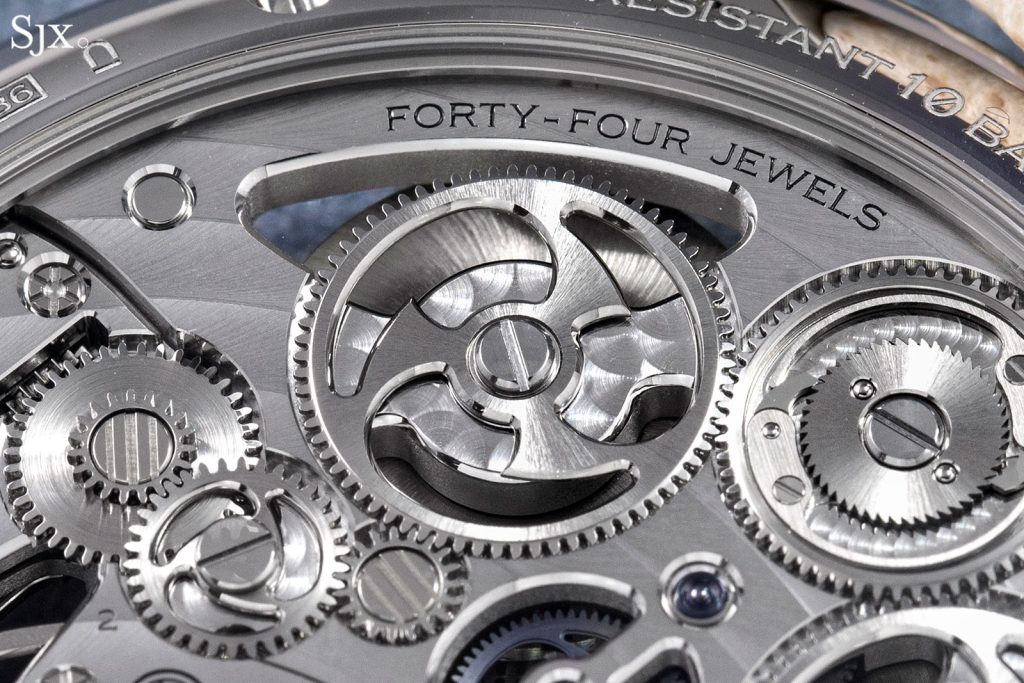
On the other hand, the CNC-machined cases exhibited superior dimensional accuracy and a more uniform finish across multiple units. Yet some connoisseurs and artisans noted a slight sterility in the appearance, describing it as “too perfect,” lacking the dynamic nuances and imperfections that characterize handcrafted metalwork.
This experiment underscored a central paradox in watchmaking: the trade-off between mechanical precision and artisanal character. While CNC machining is indispensable for complex geometry and batch consistency, integrating traditional blacksmith techniques — even partially — can imbue the finished watch with soul and heritage that resonates deeply with collectors.
The Last Living Master: A Swiss Apprentice’s Journey to Japan
Perhaps the most fascinating chapter in this fusion of ancient and modern craft is the story of a Swiss watch case finisher who traveled to Japan to learn directly from the remaining masters of Tatara-inspired metalworking.
In the quiet prefectures of Japan’s Chugoku region, where Tatara steelmaking has been practiced for centuries, a handful of artisans still preserve these secrets. Among them is the last living master blacksmith who specializes not only in forging but also in the polishing and finishing techniques adapted for watch cases and fine metalwork.
Recognizing the irreplaceable value of this tradition, Grand Seiko’s parent company and several independent Swiss ateliers arranged for select apprentices to train under this master. One such apprentice, Pierre Dubois, a seasoned finisher from the Swiss Jura, recounted his immersive experience.
Pierre described beginning his training by learning the foundations of clay furnace management and iron sand smelting — processes far removed from watchmaking yet essential to understanding the spirit of Tatara steel. Only after months of observing and assisting in the forge was he allowed to handle the delicate finishing stages, involving hand hammering, filing, and Zaratsu-style polishing on prototype watch cases.
The transition was humbling. Pierre noted that the rhythm of the hammer strikes and the nuance of the polishing strokes required a mindfulness akin to meditation — a far cry from the regimented, high-speed processes familiar in Swiss factories.
This apprenticeship was more than technical training; it was a cultural exchange and a bridging of heritage. Pierre now incorporates these techniques into select projects back home, blending Swiss precision with Japanese artistry to produce cases that are unique both in appearance and story.
His journey symbolizes the larger movement in watchmaking that values history, craftsmanship, and the human touch in an era dominated by automation and digital fabrication.
A Living Tradition Shaping the Future
The integration of the 400-year-old Tatara blacksmith technique into modern watch case finishing is more than a nod to tradition—it is a powerful statement about the value of craft and cultural continuity in luxury watchmaking. While precision machining will continue to dominate production for its efficiency and scalability, the enduring appeal of artisanal finishing lies in its capacity to connect wearer and maker, present and past.
Grand Seiko’s success in melding Tatara’s ethos with contemporary Zaratsu polishing sets a precedent for how ancient techniques can enrich modern manufacturing. It reminds us that even in the most advanced technologies, there is room—and demand—for the warmth, imperfection, and soul of human hands and centuries-old knowledge.
For collectors and enthusiasts, watches finished using these combined methods become not only timekeepers but tangible stories of resilience, artistry, and cross-cultural collaboration—reminders that sometimes, the best way forward is by embracing the lessons of the past.