In 2025, the horological world stands at a seismic crossroads. On one side lies centuries of Swiss tradition, where master watchmakers, armed with loupe and lathe, spend years perfecting the soul of a mechanical movement. On the other, a new force is rising—AI-assisted watchmaking. Fueled by data, machine learning, and computational modeling, AI is not just aiding production; it is designing movements that outperform even the most skillfully tuned calibers.
The debate is no longer theoretical. It is here, ticking quietly but precisely on the wrists of early adopters, and it is forcing the watch industry to ask profound questions: Can software replicate soul? Should hand-finishing give way to algorithmic efficiency? And what does it mean to be a watchmaker in a world where machines now craft the heartbeat of time?
Technical Comparison: AI-Designed Movements vs Hand-Regulated Craftsmanship
One of the most staggering breakthroughs in AI watchmaking is the development of ultra-precise mechanical movements engineered entirely by algorithms. In recent trials, AI-optimized calibers achieved a daily deviation of ±0.1 seconds—unheard of even in the best COSC-certified chronometers. To achieve this, AI systems analyzed decades of movement data, vibration patterns, materials stress, and atmospheric influence simulations to generate movement architectures with perfect mechanical resonance and minimal energy loss.
Traditional mechanical watches, even when hand-regulated by expert watchmakers, typically achieve ±2 to ±6 seconds per day. The art of “timing a watch” is often based on adjusting the balance wheel and escapement through feel, experience, and iterative trial-and-error. These are skills passed down through generations and are central to the romance and mythos of Swiss watchmaking.
But when AI enters the equation, subjectivity is eliminated. Algorithms can simulate millions of balance wheel designs in seconds, predict how lubricants behave over a 10-year period, and optimize gear ratios with mathematical certainty. And once the algorithm finds the optimal design, robotic micromachining units can manufacture components to tolerances as fine as 0.01 microns.
While traditionalists argue that this precision lacks “character,” the reality is that AI movements are not only more accurate but also more efficient, requiring less torque and offering longer power reserves—up to 100 hours on a single barrel. Even complications like perpetual calendars and tourbillons have been reengineered by AI to function with fewer components and improved reliability.
The battle, then, is not about capability. AI has proven it can outperform humans in raw horological metrics. The debate lies in value—emotional, historical, and cultural.
Cultural Clash: Can the Geneva Seal Embrace Algorithmic Finishing?
The Geneva Seal, or Poinçon de Genève, is one of the most prestigious certifications in the watch world. It represents the pinnacle of traditional craftsmanship, awarded only to movements assembled and finished by hand in the Canton of Geneva. But with AI and machine-finishing reaching levels indistinguishable from human work under most loupes, the rules are now being questioned.
Some argue the Geneva Seal should evolve, allowing algorithmically optimized parts and AI-regulated movements, provided the final assembly and inspection remain human-led. Others vehemently oppose the idea, claiming it would undermine the very spirit of artisanal horology. After all, can a watch truly bear the mark of Geneva if its bridges were shaped by a machine learning model trained on vibration data?
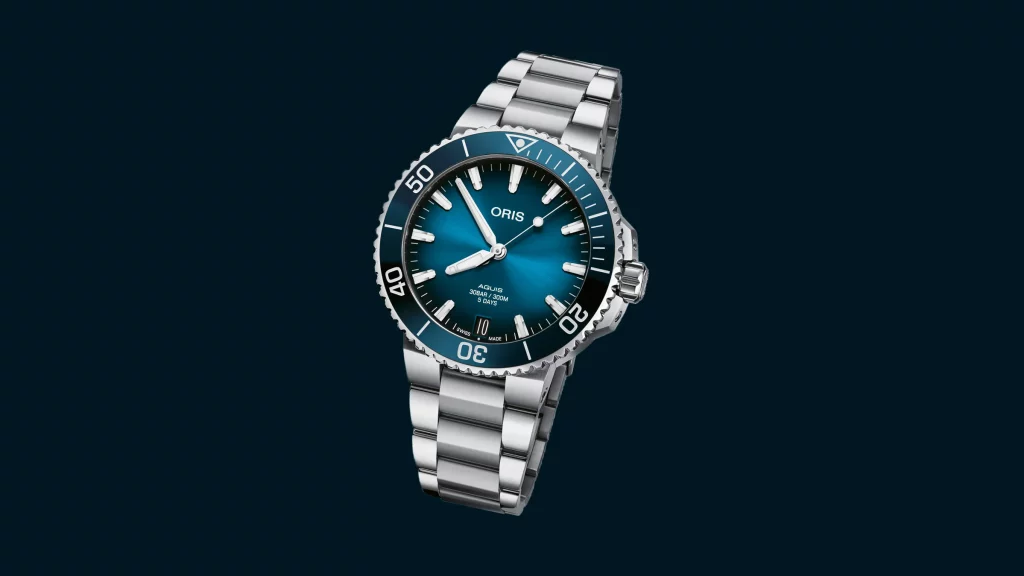
Proponents of change point to the growing number of AI-enhanced movements entering the market with exceptional finishing—Côtes de Genève applied by robot-guided tools, anglage polished to perfection by CNC-controlled buffing arms, and even guilloché patterns generated by neural networks trained on 18th-century archives.
One provocative case in 2025 came from a startup based in Neuchâtel, which submitted an AI-designed tourbillon for Geneva Seal certification. The movement was assembled and regulated by hand but digitally conceived and machine-finished. Despite its impeccable results and aesthetic brilliance, the application was denied on the basis that the movement lacked “human intent” in its design.
This incident sparked a fiery debate in Swiss watchmaking circles. Should the Seal adapt to reflect evolving craftsmanship? Or must it remain a sanctuary of purely manual art in an era increasingly shaped by code?
Future Outlook: Will Watchmakers Still Have a Job in Five Years?
With AI now capable of designing, optimizing, and even finishing movements, the role of the traditional watchmaker is undeniably shifting. But will it disappear? Not likely. Instead, the profession is bifurcating into two distinct paths—one rooted in digital fluency, the other in analog purity.
- The Hybrid Horologist
Future watchmakers will need to blend craftsmanship with code. They will use AI tools to simulate movement dynamics, program robotic tools for component finishing, and understand how to tweak algorithmic designs for artistic or ergonomic goals. Think of them as horological architects who code and carve with equal proficiency. - The Artisan Conservator
In response to the AI wave, there will also be a resurgence in purely handmade watches—pieces that celebrate human imperfection as a mark of authenticity. These timepieces will hold cultural and emotional value precisely because they resist automation. Just as vinyl records or film photography retain charm in the digital age, fully human-made watches may gain prestige as expressions of individuality. - The Curator-Engineer
Another emerging role is that of the technical curator—experts who evaluate AI-generated watches not just for mechanical quality but for conceptual merit. They judge the creativity embedded in code, the aesthetic narratives behind generative movement patterns, and the symbolic relevance of computational design. In essence, they treat AI watchmaking as an art form.
The real threat is not to the watchmaker, but to the rigid hierarchies of tradition that resist technological integration. Forward-thinking maisons are already investing in AI-literate apprenticeships, where young watchmakers learn both handcraft and programming, bridging the generational divide.
From tradition to transformation
AI watchmaking is not replacing Swiss tradition—it’s challenging it to evolve. Just as quartz once threatened mechanical horology only to give rise to a mechanical renaissance, AI may act as a catalyst for rediscovery, innovation, and redefinition.
For the collector, the question shifts from “Is it handmade?” to “What story does this piece tell?” Some will chase the perfection of AI-regulated precision. Others will seek the fingerprint of a watchmaker’s hand. And many will look for timepieces that balance both—the cold certainty of machine intelligence and the warm imperfection of human touch.
As we look toward the next five years, one thing is certain: the ticking heart of horology is now beating in both silicon and steel.